QR Code
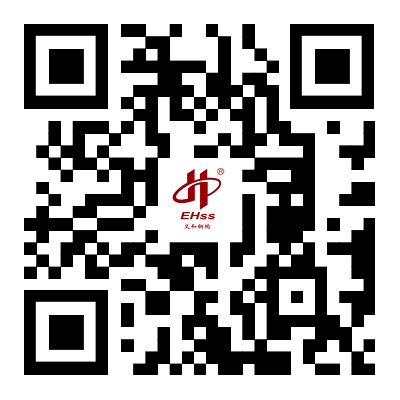
Des produits
Contactez-nous
Téléphone
E-mail
Adresse
N ° 568, Yanqing First Class Road, Jimo High-Tech Zone, Qingdao City, Province du Shandong, Chine
Bâtiment d'ingénierie en structure métalliqueest connu comme le projet vert du 21ème siècle, la structure en acier présente de nombreux avantages tels qu'une résistance élevée, une forte capacité de chargement, un poids léger, un petit volume d'espace occupé, une fabrication et une installation faciles des composants, une économie de bois, etc. de plus en plus largement utilisé dans les bâtiments industriels et civils. Les bâtiments à ossature d'acier et les entrepôts à structure métallique sont partout.
Avec le développement rapide de l'industrie, la résistance à la corrosion de l'acier et la faible résistance à la rouille et à la corrosion ainsi que d'autres problèmes sont progressivement apparus, en particulier dans les zones côtières, et l'industrie chimique est devenue un problème majeur !
La corrosion de la structure en acier entraîne non seulement des pertes économiques, mais présente également un danger caché pour la sécurité de la structure, et les accidents techniques causés par la corrosion de l'acier sont fréquents. Le traitement anticorrosion de la structure en acier (en particulier des composants en acier à paroi mince) est d'une grande importance économique et sociale, et voici quelques introductions et discussions sur les problèmes rencontrés dans le processus de construction et certaines méthodes de traitement.
1. Principales causes de corrosion des structures en acier
La prévention de la corrosion de l’acier commence par la compréhension des causes de la corrosion de l’acier.
1.1 Mécanisme de corrosion de l'acier à température ambiante (inférieure à 100°C)
La corrosion de l’acier à température ambiante est principalement une corrosion électrochimique. Les structures en acier sont utilisées dans l'atmosphère à température ambiante et l'acier est corrodé par l'action de l'humidité, de l'oxygène et d'autres polluants (scories de soudage non nettoyées, couche de rouille, saleté de surface) présents dans l'atmosphère. L'humidité relative de l'atmosphère est inférieure à 60 %, la corrosion de l'acier est très légère ; mais lorsque l'humidité relative augmente jusqu'à une certaine valeur, le taux de corrosion de l'acier augmente soudainement, et cette valeur est appelée humidité critique. À température ambiante, l'humidité critique générale de l'acier est de 60 % à 70 %.
Lorsque l'air est pollué ou salé dans l'air dans les zones côtières, l'humidité critique est très faible, la surface de l'acier forme facilement un film d'eau. À l'heure actuelle, les scories de soudage et la couche de rouille non traitée (oxyde de fer) servent de cathode, les composants de la structure en acier (matériau de base) servent d'anode dans la corrosion électrochimique du film d'eau. L'humidité atmosphérique adsorbée sur la surface de l'acier pour former un film d'eau est le facteur déterminant de la corrosion de l'acier ; l'humidité relative de l'atmosphère et la teneur en polluants sont des facteurs importants affectant le degré de corrosion atmosphérique.
1.2 Mécanisme de corrosion de l'acier à haute température (au-dessus de 100℃)
La corrosion de l’acier à haute température est principalement une corrosion chimique. A haute température, l'eau existe à l'état gazeux, l'effet électrochimique est très faible, réduit à un facteur secondaire. Contact de métal et de gaz secs (tels que O2, H2S, SO2, Cl2, etc.), génération de surface des composés correspondants (chlorures, sulfures, oxydes), formation de corrosion chimique de l'acier.
2 Méthodes de protection contre la corrosion des structures en acier
Selon le principe électrochimique de la corrosion de l'acier, tant que la formation d'une batterie de corrosion est empêchée ou détruite ou que les processus cathodiques et anodiques sont fortement bloqués, la corrosion de l'acier peut être évitée. L'utilisation de la méthode de la couche protectrice pour empêcher la corrosion de la structure en acier est une méthode courante à l'heure actuelle. La couche protectrice couramment utilisée est des types suivants :
2.1 Couche de protection métallique: la couche protectrice métallique est un métal ou un alliage ayant un effet protecteur cathodique ou anodique, par galvanoplastie, placage par pulvérisation, placage chimique, placage à chaud et placage par infiltration et d'autres méthodes, la nécessité de protéger la surface métallique pour former une couche protectrice métallique (film) pour isoler le métal du milieu corrosif en contact avec le milieu corrosif, ou utiliser l'effet protecteur électrochimique de la protection métallique, de manière à empêcher la corrosion.
2.2 Couche protectrice: par des méthodes chimiques ou électrochimiques pour créer la surface de l'acier afin de générer un film composé résistant à la corrosion, afin d'isoler le milieu corrosif et le contact métallique, afin d'éviter la corrosion du métal.
2.3 Couche protectrice non métallique: avec des peintures, des plastiques, de l'émail et d'autres matériaux, par peinture, pulvérisation et autres méthodes, pour former un film protecteur sur la surface du métal, de sorte que le métal et les milieux corrosifs soient isolés, de manière à empêcher la corrosion du métal .
3. Traitement de surface en acier
Avant le traitement de l'acier en usine, la surface des composants sera inévitablement tachée d'huile, d'humidité, de poussière et d'autres polluants, ainsi que par la présence de bavures, d'oxyde de fer, de couche de rouille et d'autres défauts de surface. D'après les principales raisons précédentes de la corrosion des structures en acier, nous savons que la teneur en polluants est un facteur important affectant le degré de corrosion atmosphérique, et les contaminants de surface affecteront sérieusement l'adhérence des revêtements sur la surface de l'acier et rendront la peinture le film sous la corrosion continue de se dilater, entraînant une défaillance ou des dommages du revêtement, incapable d'obtenir l'effet protecteur souhaité. Par conséquent, la qualité du traitement de surface de l'acier sur l'effet protecteur du revêtement et la durée de vie de l'influence, parfois même plus que le revêtement lui-même, diverses différences de performances dans l'impact des aspects suivants doivent être soulignées :
3.1. Pour les composants porteurs difficiles à réparer pendant la période de service, le degré de détartrage doit être augmenté en conséquence.
3.2. Avant et après le détartrage, la graisse, les bavures, les peaux médicinales, les éclaboussures et l'oxyde de fer doivent être soigneusement éliminés.
3.3. la réception qualité des travaux de détartrage et de peinture sera conforme à la réglementation.
4. Revêtement anticorrosion
Les revêtements anticorrosion sont généralement composés d'un primaire et d'un top coat. Apprêt dans la poudre plus, moins de matériau de base, film rugueux, la fonction de l'apprêt est de rendre le film de peinture avec le niveau de base et la combinaison de couche de finition solide, c'est-à-dire d'avoir une bonne adhérence ; l'apprêt contient des pigments inhibiteurs de corrosion, peut empêcher l'apparition de corrosion, et certains peuvent également être une passivation du métal et une protection électrochimique pour empêcher le métal de rouiller. La couche de finition est moins de poudre, plus de matériau de base, une fois le film brillant, la fonction principale est de protéger la couche inférieure d'apprêt, elle doit donc être imperméable à l'atmosphère et à l'humidité, et doit être capable de résister à la décomposition physique et chimique. causée par les intempéries. La tendance actuelle est d’utiliser des résines synthétiques pour améliorer la résistance du support aux intempéries. Les revêtements anticorrosion résistants aux conditions atmosphériques ne résistent généralement qu'à la corrosion en phase vapeur dans l'atmosphère. Pour les endroits sujets à la corrosion par les acides, les alcalis et d'autres milieux, des revêtements résistants aux acides et aux alcalis doivent être utilisés.
La peinture anticorrosion selon la fonction de protection peut être divisée en apprêt, peinture intermédiaire et couche de finition, chaque couche de peinture a ses propres caractéristiques, chacune responsable de sa propre responsabilité, la combinaison des couches, la formation d'un revêtement composite pour améliorer les performances anticorrosion, prolonger la durée de vie.
4.1amorces
La couche d'apprêt les revêtements anticorrosion couramment utilisés sont un apprêt riche en zinc et un apprêt époxy rouge fer, la peinture riche en zinc est composée d'un grand nombre de poudre de zinc microfine et d'une petite quantité de matériaux filmogènes. Les propriétés électrochimiques du zinc sont supérieures à celles de l'acier et, lorsqu'il est soumis à la corrosion, il a un effet « d'abnégation », de sorte que l'acier est protégé. Le produit de corrosion, l'oxyde de zinc, remplit les pores et rend le revêtement plus dense. Les apprêts riches en zinc couramment utilisés sont des trois types suivants :
(1) apprêt inorganique riche en zinc pour verre soluble, c'est du verre soluble comme matériau de base, ajouter de la poudre de zinc, mélanger et brosser, après durcissement pour être rincé à l'eau, le processus de construction est complexe, conditions de processus difficiles, le traitement de surface doit être dans le Sa2,5 ou plus, en plus des exigences de température ambiante et d'humidité, la formation du film de revêtement est facile à craquer, à peler et a été rarement utilisée.
(2) apprêt inorganique soluble riche en zinc, l'apprêt est à base d'orthosilicate d'éthyle, d'alcool comme solvant, polymérisation partiellement hydrolysée, ajouter de la poudre de zinc mélangée à un film uniformément enduit.
(3) apprêt riche en zinc, il s'agit d'une résine époxy comme matériau de base filmogène, ajoutant de la poudre de zinc, durcissant pour former un revêtement. L'apprêt époxy riche en zinc présente non seulement d'excellentes propriétés anticorrosion et une forte adhérence, mais avec le prochain revêtement, la peinture époxy à nuage de fer est un bon type d'adhérence. Principalement utilisé dans l’atmosphère générale de la structure en acier et de la corrosion des équipements pétrochimiques.
L'apprêt époxy rouge à l'oxyde de fer est divisé en boîtes de peinture à deux composants, le composant A (peinture) en résine époxy, l'oxyde de fer rouge et d'autres pigments antirouille, agent de durcissement, agent anti-enfoncement, etc., le composant B est un agent de durcissement, la construction de la proportion du déploiement. L'oxyde de fer rouge est une sorte de pigment antirouille physique, sa nature est stable, son fort pouvoir couvrant, ses particules fines, peut jouer un bon effet de protection dans le film de peinture, a de bonnes performances antirouille. L'apprêt rouge à l'oxyde de fer époxy sur la plaque d'acier et la couche supérieure de peinture époxy ont une bonne adhérence, un séchage rapide à température ambiante, la couche supérieure de peinture de surface ne déteint pas, plus couramment utilisée dans les pipelines en acier, les réservoirs, les projets anticorrosion de structures en acier. , comme apprêt antirouille.
4.2 couche intermédiaire de peinture
La peinture de la couche intermédiaire est généralement une peinture époxy au mica et à l'échelle de verre époxy ou une peinture époxy épaisse en suspension. La peinture époxy mica est fabriquée à partir de résine époxy comme matériau de base en ajoutant de l'oxyde de fer mica, la microstructure de l'oxyde de fer mica est comme du mica feuilleté, son épaisseur n'est que de quelques micromètres et son diamètre est de dizaines de micromètres à cent micromètres. Il s'agit d'une résistance à haute température, d'une résistance aux alcalis, d'une résistance aux acides, non toxique, la structure en flocons peut empêcher la pénétration moyenne, des performances anti-corrosion améliorées et un faible retrait, une rugosité de surface, est une excellente couche intermédiaire de peinture anti-corrosion. La peinture à l'échelle de verre époxy est une résine époxy comme matériau de base, avec de l'échelle de verre écailleuse comme agrégat, ainsi qu'une variété d'additifs composés d'une peinture anticorrosion épaisse de type palette. L'épaisseur du tartre de verre n'est que de 2 à 5 microns. Comme les écailles sont disposées en couches au-dessus et en dessous du revêtement, une structure de protection unique se forme.
4.3 couche de finition
Les peintures utilisées pour les couches de finition peuvent être divisées en trois qualités selon leurs prix :
(1) La qualité ordinaire est la peinture époxy, la peinture en caoutchouc chloré, le polyéthylène chlorosulfoné, etc.
(2) La qualité moyenne est une peinture polyuréthane ;
(3) La qualité supérieure est la peinture polyuréthane modifiée au silicone, la couche de finition acrylique modifiée au silicone, la peinture au fluor, etc.
Peinture époxy après durcissement chimique, stabilité chimique, revêtement dense, forte adhérence, propriétés mécaniques élevées, elle résiste aux acides, aux alcalis, au sel, peut résister à une variété de corrosions chimiques.
5. Le choix de la peinture anticorrosion doit prendre en compte plusieurs points
5.1 Il convient de tenir compte de la cohérence des conditions d'utilisation de la structure et de la gamme de peintures sélectionnées, en fonction du milieu corrosif (type, température et concentration) phase gazeuse ou phase liquide, zones chaudes et humides ou zones sèches et autres conditions de sélection. Pour un milieu acide, une peinture à base de résine phénolique avec une meilleure résistance aux acides peut être utilisée, tandis que pour un milieu alcalin, une peinture à base de résine époxy avec une meilleure résistance aux alcalis doit être utilisée.
5.2 Les possibilités des conditions de construction doivent être prises en compte. Certains conviennent au brossage, certains conviennent à la pulvérisation, certains conviennent au séchage naturel pour former un film, etc. Pour les conditions générales, il est conseillé d’utiliser une peinture sèche et facile à pulvériser, prenant à froid.
5.3 Tenir compte de la correspondance correcte des revêtements. Comme la plupart de la peinture est un matériau colloïdal organique comme matériau de base, peignez chaque couche de film, il existe inévitablement de nombreux supports microporeux et corrosifs exceptionnellement petits qui peuvent encore pénétrer dans l'érosion de l'acier. Par conséquent, la construction des peintures actuelles ne consiste pas à appliquer une seule couche, mais à appliquer plusieurs couches, le but étant de réduire les micropores au minimum. Il doit y avoir une bonne adaptabilité entre l'apprêt et la couche de finition. Tels que la peinture au chlorure de vinyle et l'apprêt phosphatant ou l'apprêt alkyde rouge de fer supportant l'utilisation de bons résultats, et ne peuvent pas être utilisés avec un apprêt à base d'huile (tel que la peinture rouge à base d'huile) supportant l'utilisation. Étant donné que la peinture au perchloroéthylène contient des solvants puissants, elle détruira le film d'apprêt.
Il est d'une grande importance de faire du bon travail en matière d'antirouille et d'anticorrosion pour promouvoir le développement des bâtiments à structure métallique, économiser les matériaux, prolonger la durée de vie du bâtiment, assurer une production sûre et réduire la pollution de l'environnement.
N ° 568, Yanqing First Class Road, Jimo High-Tech Zone, Qingdao City, Province du Shandong, Chine
Copyright © 2024 Qingdao Eihe Steel Structure Group Co., Ltd. Tous droits réservés.
Links | Sitemap | RSS | XML | Privacy Policy |
Teams